Изготовление зубчатых передач для машиностроения
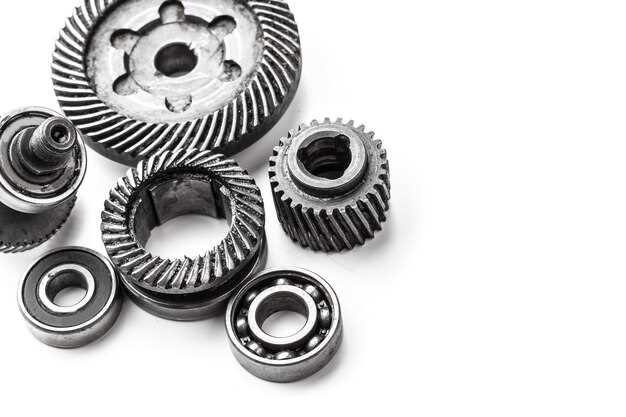
Выбор подходящего метода изготовления зубчатых передач становится ключевым шагом для повышения производительности машин. Используйте фрезерование или шлифование в зависимости от требуемой точности. Если вам нужно оптимальное решение для массового производства, обратите внимание на метод штамповки, который обеспечивает высокую скорость и низкие затраты.
Учитывайте материалы, из которых будут изготовлены передачи. Стали с высоким содержанием углерода и легированные стали обеспечивают отличные механические свойства и износостойкость. При необходимости улучшить прочность на изгиб рассмотрите использование закаленных сталей или композитных материалов.
При проектировании зубчатых передач важно учитывать режимы работы и нагрузки. Задействуйте программное обеспечение для моделирования, чтобы заранее увидеть, как передачи будут вести себя под различными условиями. Обратите внимание на параметры шестерен и модулей: размер зубьев и угол наклона влияют на эффективность передачи мощности и шумность работы механизма.
Тестируйте готовые изделия на прочность и износ. Проведение испытаний и контроль качества на всех этапах производства помогут избежать в дальнейшем дорогостоящих ремонтов и продлить срок службы оборудования.
Технологические процессы производства зубчатых передач
Начните производство зубчатых передач с выбора подходящего материала. Сталь, чугун, либо специальные сплавы – все они обладают различными механическими свойствами. Рассмотрите требования к прочности и износу, чтобы выбрать наилучший вариант.
Следующий шаг – формирование зубчатой заготовки. Обычно используется метод механической обработки. Распространены процессы токарной и фрезерной обработки. Эти методы обеспечивают необходимую точность и геометрию зубьев.
- Токарная обработка: Позволяет создать базовые контуры заготовки. Используйте высокоскоростные стали для режущих инструментов.
- Фрезерная обработка: Подходит для формирования зубьев. Используйте фрезы с несколькими зубьями для повышенной производительности.
После обработки заготовки выполните закалку для повышения прочностных характеристик. Для этого применяют закалку в масле или воде в зависимости от типа материала. После закалки проведите отпущение для снятия внутренних напряжений.
Обратите внимание на шлифовку зубьев. Этот этап необходим для достижения высокой точности и улучшения качества поверхности. Используйте шлифовальные круги с подходящей зернистостью для оптимальных результатов.
- Задайте параметры резания: скорость, подачу и глубину реза.
- Контролируйте температуру расширения деталей во время шлифовки.
- Оценивайте качество обработки через специальные измерительные инструменты.
Завершите процесс сборкой зубчатых передач. Используйте специальные смазочные материалы для предотвращения износа. Убедитесь в точности совмещения частей, чтобы избежать механических повреждений в процессе эксплуатации.
Регулярно проводите контроль качества на всех этапах производства. Это позволит избежать дефектов и повысить надежность изделия. Применяйте системы контроля, такие как ультразвуковая дефектоскопия и радиография, для проверки качества заготовок и готовых изделий.
Каждый из этих процессов требует тщательного планирования и контроля. Эффективная организация работы на каждом этапе – залог успешного производства качественных зубчатых передач.
Выбор материалов для зубчатых передач: основные критерии
Определите цель применения зубчатых передач – это поможет выбрать оптимальный материал. Если передачи работают в условиях высокой нагрузки и температур, лучше выбрать легированные стали. Для облегченных механических передач подойдут алюминиевые сплавы или пластмассы.
Оцените износостойкость выбранного материала. Стали с высоким содержанием углерода обладают отличной износостойкостью, что важно для длительного срока службы. В некоторых случаях полезно применять закаленные стали, которые увеличивают жесткость и прочность.
Не забывайте о коррозионной стойкости. В агрессивных средах выбор нержавеющих сталей вполне оправдан. Если условиях эксплуатации не требуют высокой коррозионной стойкости, то обычные углеродные стали могут быть более экономичным вариантом.
Также учитывайте технологичность материала. Легкость в обработке важна, особенно если требуется массовое производство. Некоторые сплавы сложно механически обрабатывать, что может повысить затраты на производство.
Кроме того, следите за доступностью и стоимостью материалов. Убедитесь, что выбранный материал находится в высокой доступности на рынке, чтобы избежать задержек в производстве и снизить затраты.
Наконец, стоит учитывать требования к маслостойкости и термостойкости. Для рабочих условий с постоянными колебаниями температур обязательно выбирайте специальным образом подготовленные материалы, которые сохранят свои свойства даже при высоких нагрузках и температурах.
Проверка и контроль качества зубчатых передач в машиностроении
Определите стандарты качества на каждом этапе производства зубчатых передач. Используйте методики контроля, такие как визуальная проверка, измерение геометрии зубьев и проверка зазоров. Убедитесь, что каждое изделие соответствует допустимым значениям по размерам и форме.
Применяйте стандарт ISO 6336 для оценки прочности зубчатых передач. Проводите расчеты по методике, адаптированной для конкретного типа передачи. Обязательно проверяйте допускаемое напряжение и следите за точностью обработки.
Используйте оборудование для неразрушающего контроля, например, магнитно-порошковую и ультразвуковую дефектоскопию. Эти методы помогают выявить внутренние дефекты, которые могут повлиять на долговечность и надежность зубчатых передач.
Запланируйте периодические тестирования на усталостные нагрузки. Этот процесс позволяет оценить долговечность передачи в условиях реальных нагрузок. Установите протоколы для экспериментов и фиксируйте полученные данные для последующего анализа.
Для повышения качества используйте автоматизированные системы контроля. Такие решения позволяют снизить вероятность человеческого фактора и ускорить процесс проверки. Интегрируйте автоматизированные измерительные системы в производственную линию для контроля параметров в реальном времени.
Не забывайте о документировании результатов контроля. Создание отчетов о качестве поможет выявить тенденции и причины отклонений. Анализируйте данные регулярно для улучшения процессов производства и контроля.
Обучайте сотрудников основам контроля качества. Поэтому создание команды, осведомленной о современных методах проверки, значительно повысит общие стандарты продукции и ускорит их внедрение в производство.
-
“Бэтмобиль“ из фильма Бертона уйдет с аукциона24-04-2025, 17:11 3
-
BMW представил новый светящийся концепт на автосалоне в Шанхае24-04-2025, 16:55 1
-
Как будет проходить строительство BRT в Алматы, рассказали в акимате24-04-2025, 16:26 1
-
Что изменится в жизни казахстанцев с апреля 2025 года2-04-2025, 17:26 13
-
Cколько будут платить за ОСМС казахстанцы в 2025 году5-04-2025, 16:08 8
-
ЧП на Павлодарском нефтехимическом заводе: есть пострадавшие2-04-2025, 18:16 7
-
“Лучше честно признаться“ - депутат заявила о нарушении закона Минфином5-04-2025, 15:41 6