Сталеплавильное производство технологии и процессы
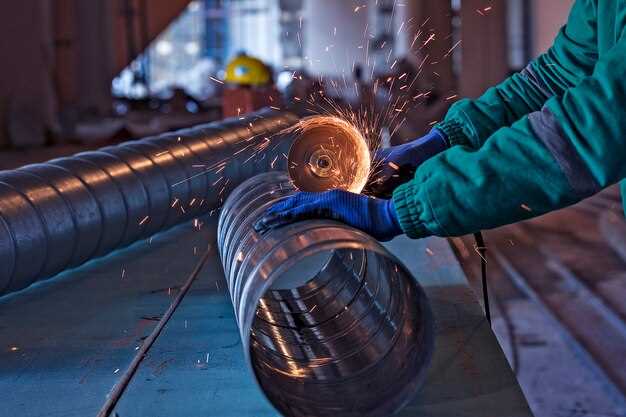
Изучите ключевые технологии сталеплавильного производства, чтобы оптимизировать процессы и повысить качество конечного продукта. Начните с современного методa электропечей, который позволяет не только достичь высокой температуры для переплавки, но и значительно сократить выбросы углекислого газа. Подходя к этому процессу с учетом автоматизации, можно существенно уменьшить затраты на электроэнергию и сырье.
Обратите внимание на использование сырья и его предварительную подготовку. Эффективное сортирование и переработка сталей позволяют сократить отходы и увеличить производительность. Применение новых сортов стали, таких как нержавеющие и легированные, позволяет расширить диапазон применения готовой продукции и улучшить её характеристики.
Не забывайте про технологии охлаждения и отжига. Правильный выбор этих процессов влияет не только на прочность, но и на пластичность стали. Внедрение контроля температуры и времени выдержки значительно улучшает механические свойства стали, позволяя добиться более высоких стандартов качества.
Сталеплавильное производство: технологии и процессы
Современные технологии в сталеплавильном производстве включают в себя несколько ключевых процессов, каждый из которых заслуживает внимания. Основным процессом является выплавка стали, которая может осуществляться различными методами, такими как кислородно-конверторный способ или электропечи.
Кислородно-конверторный метод позволяет эффективно перерабатывать полученный чугун в сталь. В процессе используются кислородные конверторы, где воздух или чистый кислород подается под давлением для снижения содержания углерода. Этот метод характеризуется высокой производительностью и низкими затратами.
Электродуговые печи применяются для переработки вторичного сырья и стали. Этот процесс использует электрическую дугу для плавления материалов, что позволяет точно контролировать температурный режим и состав. Это особенно ценно при производстве нержавеющей и легированной стали.
Рециркуляция используемых материалов, таких как шлаки, становится важным аспектом эффективного производства. Шлаки могут перерабатываться и использоваться в других процессах, что снижает затраты на сырье и минимизирует отходы.
Поддержание контроля за качеством продукции включает в себя регулярные проверки на стадии плавления и на выходе готовой стали. Использование современных технологий анализа помогает гарантировать соответствие материалов стандартам. Это позволяет избежать недочетов на производстве и обеспечивает высокую конкурентоспособность.
Автоматизация процессов, включая управление температурой и составом сталеплавильного оборудования, значительно оптимизирует работу. Системы автоматизированного контроля помогают снизить человеческий фактор и повысить точность процессов.
Эффективные методы управления энергией и ресурсами значительно снижают затраты. Внедрение возобновляемых источников энергии в сталеплавильное производство также становится все более актуальным. Использование солнечных батарей или ветряных установок для энергии обеспечивает дополнительную экономию и поддержку устойчивого развития.
Инвестирование в современные технологии и оборудование увеличивает производительность и снижает экологическую нагрузку. Сфокусировавшись на оптимизации процессов и инновациях, производители могут достичь значительных результатов в этом конкурентном секторе. Развитие новых технологий, таких как гидрометаллургия, может стать следующим шагом на пути к улучшению сталеплавильного производства.
Технология электросталеплавильного производства
Электросталеплавильные установки используют электродные печи для получения стали из металлолома и железорудного сырья. Основной процесс заключается в плавлении металла при помощи электрического разряда, который происходит между графитовыми электродами и металлическойCharge. Это обеспечивает высокую точность в регулировании температуры и состава сплава.
Основное внимание уделите выбору типа печи. Существует несколько вариантов: печи с прямым и обратным током. Печи с прямым током обеспечивают более стабильный процесс плавления и сокращают продолжительность операции. Обратные печи более универсальны, подходящие для различных видов сырья.
Рекомендуется тщательно подбирать состав Charge. Использование качественного металлолома, а также добавление легирующих элементов, таких как марганец и хром, значительно улучшает характеристики конечного продукта. Контроль за химическим составом можно осуществлять на различных стадиях процесса, что позволяет вовремя корректировать параметры производства.
Оптимизация режима плавления позволяет значительно снизить расход электроэнергии. Регулярная проверка работы электрода, а также использование электронных систем управления помогут поддерживать необходимые параметры, что способствует увеличению выхода продукции.
После плавления сталь отливается в формы или подается на дальнейшую переработку. Контроль за качеством на этом этапе также является важной составляющей. Это может включать анализ механических свойств материала как до, так и после отливки.
На последующем этапе охлаждения стоит применять методы, которые обеспечивают равномерное охлаждение для избежания образования ненужных напряжений в материале. Важно иметь в наличии системы контроля температуры и механических свойств, чтобы гарантировать высокое качество готовой продукции.
Процессы получения и очистки стали в конвертерном производстве
Конвертерное производство стали включает в себя несколько ключевых процессов, позволяющих получить качественный металл. Основные этапы – это выплавка, охлаждение и очистка. Каждая стадия важна для достижения желаемых характеристик конечного продукта.
На первом этапе реализации процесса выплавки сырьё, как правило, включает чугун и легирующие элементы. Здесь активно используется процесс кислородной выплавки, который обеспечивает быстрое окисление примесей. Кислород подаётся в жидкий чугун, что способствует удалению углерода и других нежелательных элементов.
- Оптимальная температура для выплавки – около 1600 °C, что позволяет эффективно удалять примеси.
- Длительность процесса составляет 20-50 минут в зависимости от исходного состава чугуна.
Следующий этап – это очистка стали от газов и шлака. Это важная стадия, которая влияет на механические свойства готового металла.
- Выбор шлакосъемной операции. Обычно используются методики осадительной и пневматической очистки.
- Интенсификация удаления шлака осуществляется за счёт добавления флюсов, таких как известь или флюорит. Это помогает эффективно извлекать загрязняющие элементы.
Кроме того, некоторые производственные линии используют рециркуляцию шлака, что позволяет снижать затраты на материалы и повышать экологичность процесса. Для этого обычно применяются схемы, позволяющие повторно использовать шлак в процессе плавки.
После завершения очистки сталь заливают в форму для охлаждения. Этот процесс часто проходят в специальных криогенных установках, что помогает предотвратить появление внутренних дефектов.
Управление качеством на каждом этапе включает в себя лабораторные анализы состава, что позволяет настраивать параметры процессов. Поддержание контроля качества в конвертерном производстве обеспечивает получение стали с заданными характеристиками.
Таким образом, каждый этап от получения до очистки стали в конвертерном производстве требует точной настройки и высококачественного сырья, что в конечном итоге гарантирует надёжность и долговечность металлических изделий.
Инновации и автоматизация в сталеплавильных технологиях
Автоматизация процессов контроля качества стали обеспечивает точность и стабильность продукции. Используйте системы машинного зрения для обнаружения дефектов на ранних стадиях. Это позволяет сократить количество бракованных партий и повысить общую удовлетворенность клиентов.
Внедрение роботизированных систем в плавильные процессы снижает трудозатраты и риски для сотрудников. Роботы могут выполнять такие операции, как загрузка шихты и управление печами, что значительно ускоряет циклы производства и минимизирует время простоя.
Новые технологии терморегулирования, такие как системы управления температурой, позволяют оптимизировать процессы выплавки. Они поддерживают стабильный температурный режим, что улучшает свойства стали и снижает расход электроэнергии.
Используйте анализ больших данных для прогнозирования потребностей в производстве. Интеграция аналитических систем помогает выявлять тенденции и повышать производительность за счет оптимизации графиков производства.
Внедрение технологий искусственного интеллекта для прогнозирования поломок оборудования уменьшает время простоя и затраты на ремонт. Такие системы могут предсказывать неисправности на основе анализа исторических данных и текущих показателей.
Рассмотрите возможность использования аддитивных технологий для создания прототипов и запчастей. Это сокращает время на разработку и производство уникальных компонентов для сталеплавильных процессов.
Интеграция интернета вещей (IoT) в систему управления производственными процессами обеспечивает удаленный мониторинг и диагностику. Это позволяет своевременно реагировать на изменения и улучшать общую эффективность работы.
Поддерживайте постоянное обучение сотрудников по новым технологиям. Регулярные курсы повышения квалификации помогут вашим специалистам эффективно использовать новые инструменты и методы в работе.
-
Павлодар в шоке: уличная агрессия с ножами и палками обернулась задержанием9-06-2025, 21:27 6
-
Что скрывает павлодарский ресторан: два банкета — два отравления?10-06-2025, 18:44 2
-
Что скрывает трагедия в павлодарском такси?25-05-2025, 16:27 80
-
Кто скрывается за владельцами аэропортов Павлодара и Кокшетау?2-06-2025, 11:14 11
-
Как миллиард исчез из банка: тайна раскрыта?28-05-2025, 15:27 9
-
Как в Казахстане раскрыли тайны подпольного мира?29-05-2025, 20:27 8