Эксплуатация и ремонт котлотурбинного оборудования
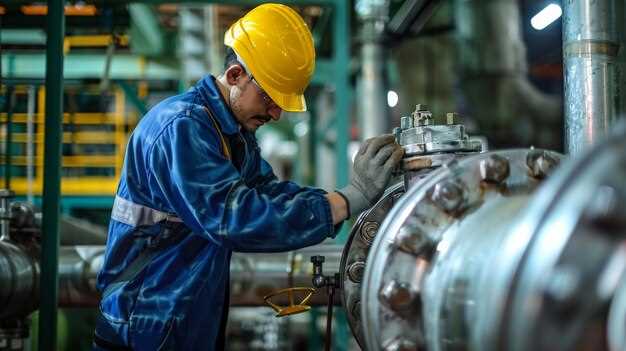
Чтобы обеспечить надежную работу котлотурбинного оборудования, необходимо регулярно проводить его осмотр и обслуживание. Начните с диагностики основных компонентов, таких как паровые котлы, турбины и системы управления, чтобы выявить потенциальные неисправности. Инвестируйте в качественные инструменты для анализа состояния оборудования, такие как ультразвуковые толщиномеры и виброметры.
При возникновении неисправностей действуйте быстро. Заменяйте изношенные детали с учетом рекомендуемых производителем спецификаций. Обратите внимание на контроль за эффективностью топливного использования: неправильная настройка котла может привести к значительным потерям. Использование автоматизированных систем управления позволит сократить время простоя и улучшить качество энергии.
Запланированное техническое обслуживание также играет важную роль. Создайте график, который включает в себя регулярные проверки и профилактическое обслуживание. Это поможет предотвратить неожиданные поломки и значительно продлит срок службы оборудования. Не забывайте обучать сотрудников правилам эксплуатации и основам диагностики, что повысит уровень ответственной работы.
Наконец, внедрение современных технологий, таких как системы мониторинга в реальном времени, поможет своевременно реагировать на изменения в работе оборудования. Это, в свою очередь, обеспечит стабильность и безопасность в процессе его эксплуатации.
Этапы эксплуатации котлотурбинного оборудования: от ввода в эксплуатацию до планового обслуживания
С момента ввода в эксплуатацию котлотурбинного оборудования важно следовать четкому плану. Первым шагом является детальное обследование и тестирование всех систем. Убедитесь, что оборудование соответствует техническим характеристикам и требованиям безопасности. Проведите все необходимые настройки, чтобы обеспечить стабильность работы в дальнейшем.
На этапе эксплуатации активно контролируйте параметры работы оборудования. Установите регулярные мониторинги температуры, давления и уровня топлива. Используйте автоматизированные системы для сбора данных, что упростит анализ и быстрое реагирование на возможные отклонения.
Для поддержания работоспособности проводите профилактическое обслуживание через определенные промежутки времени. Основные процедуры включают очистку фильтров, проверку уплотнений и диагностику насосных систем. Используйте специальное оборудование для проведения детальных проверок, что поможет выявить потенциальные проблемы на ранних стадиях.
Планируйте ревизию котлов и турбин с интервалами, определенными производителем. Это включает в себя ремонтные работы, замену изношенных деталей и проверку систем управления. При этом не забудьте вести строгий учёт всех выполненных работ и запасных частей.
Наконец, после каждого основного обслуживания анализируйте результаты работы. Это даст возможность оценить эффективность проведённых мероприятий и внести коррективы в эксплуатационные процедуры. Такой подход позволит поддерживать оборудование в наилучшей форме и продлить его срок службы.
Основные методы диагностики неисправностей котлотурбинного оборудования
Применяйте термографию для выявления перегревов в коттах и турбинах. Этот метод позволяет быстро выявить участки, где температура выходит за норму, что может свидетельствовать о проблемах с теплообменом или нарушениях в изоляции.
Используйте вибрационный анализ для определения состояния вращающихся частей оборудования. Неравномерные вибрации могут сигнализировать о несбалансированности механических узлов, что требует немедленного вмешательства.
Проводите ультразвуковые испытания для обнаружения утечек воздуха и пара в системах. Эти утечки приводят к снижению КПД оборудования и увеличению затрат на энергоресурсы. Ультразвук помогает точно локализовать проблемы.
Примените методы акустической эмиссии. Захватывая звук, который издают материал или механизмы при механических нагрузках, можно выявить внутренние дефекты до их критического развития.
Не забывайте об электро-магнитных измерениях. Они эффективны для диагностики состояния изоляции электродвигателей и генераторов. Выявление проблем на начальной стадии предотвращает более серьезные неисправности.
Регулярно проводите визуальные осмотры оборудования. Простые методы, такие как осмотр на наличие коррозии, трещин и других видимых повреждений, помогают вовремя замечать опасные сигналы.
Если требуется более глубокое обследование, применяйте методы рентгенографического контроля. Этот подход позволяет получить внутренние изображения и выявлять скрытые дефекты сварных швов и структурных элементов.
Интеграция данных из различных методов позволяет получить полное представление о состоянии котлотурбинного оборудования. Используйте эту информацию для планирования ремонтных работ и повышения надежности в эксплуатации.
Современные технологии и материалы для ремонта котлотурбинного оборудования
Для повышения надежности работы котлотурбинного оборудования применяйте методы, основанные на аддитивных технологиях. 3D-печать позволяет быстро создавать запасные части и элементы, что сокращает время простоя. Используйте порошковые металлы для печати деталей, которые требуют высокой прочности и устойчивости к коррозии.
Керамические покрытия защищают поверхности от воздействия высоких температур и агрессивной среды. Используйте материалы с низким коэффициентом трения для уменьшения износа и повышения долговечности. Данные технологии подходят для роторов и статоров, увеличивая срок службы компонентов.
Для ремонта трубопроводов и конденсаторов внедряйте технологии холодной сварки. Это решение отличает скорость применения и отсутствие необходимости в нагреве. Специальные составы позволяют восстановить целостность конструкций за короткое время без дополнительной обработки.
Используйте композитные материалы для замены традиционных металлов. Они обеспечивают меньший вес и большую прочность. Например, углеволокно находит применение в детали, подверженные высоким механическим нагрузкам.
Для оценки состояния оборудования применяйте метод ультразвуковой диагностики. Этот способ позволяет не разбирать конструкцию, что экономит время и ресурсы. С его помощью можно выявить трещины, коррозию и другие дефекты на начальных стадиях.
Рекомендовано проводить регулярный мониторинг с использованием датчиков давления и температуры, чтобы оперативно реагировать на изменения. Эти данные помогают предсказывать возможные отказы и планировать техническое обслуживание.
Современные решения, такие как инфракрасная термография, помогут выявить перегрев элементов, а при использовании вибрационного мониторинга можно определить несоответствие в работе компонентов. Инвестируйте в оборудование для диагностики, это окупится в виде уменьшения затрат на ремонт и повышения надежности системы.
-
“Бэтмобиль“ из фильма Бертона уйдет с аукциона24-04-2025, 17:11 3
-
BMW представил новый светящийся концепт на автосалоне в Шанхае24-04-2025, 16:55 1
-
Как будет проходить строительство BRT в Алматы, рассказали в акимате24-04-2025, 16:26 1
-
Что изменится в жизни казахстанцев с апреля 2025 года2-04-2025, 17:26 13
-
Cколько будут платить за ОСМС казахстанцы в 2025 году5-04-2025, 16:08 8
-
ЧП на Павлодарском нефтехимическом заводе: есть пострадавшие2-04-2025, 18:16 7
-
“Лучше честно признаться“ - депутат заявила о нарушении закона Минфином5-04-2025, 15:41 6